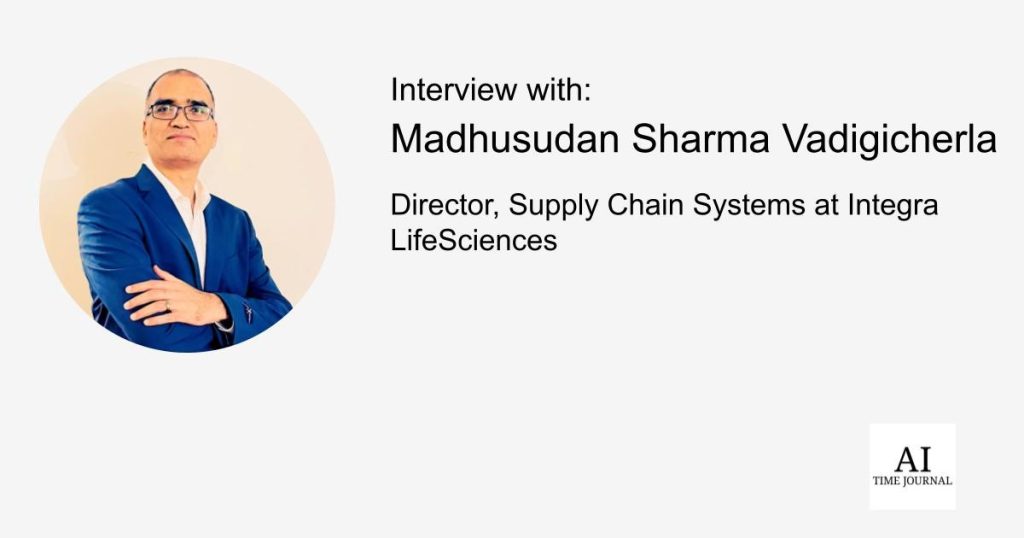
In this insightful interview, Madhusudan Sharma Vadigicherla, Director of Supply Chain Systems at Integra LifeSciences, explores the transformative role of artificial intelligence in the supply chain industry. As businesses face growing complexity and volatility, Madhusudan delves into how AI is reshaping key areas such as logistics, procurement, and data governance. He also shares his perspective on the future of AI technologies, the importance of leadership in driving digital transformation, and the challenges organizations face in adapting to a rapidly evolving landscape. Read on for an in-depth discussion on AI’s potential to revolutionize supply chain operations.
Discover more interviews like this here: Manasi Vartak on Realizing the Power of Data and Predictive Technologies, AI Governance, Women in AI, and More
How do you see artificial intelligence transforming supply chain operations in the next five years, and what key trends should businesses prepare for?
Human in the loop is Phasing out and the businesses are slowly transitioning to Human on the loop and Human out of the loop. Artificial intelligence (AI) is poised to revolutionize supply chain operations within the next five years through several key advancements. These transformative changes are expected to reshape the industry landscape and drive unprecedented levels of efficiency, productivity, and innovation. AI-powered algorithms will analyze vast amounts of historical data, market trends, and external factors to predict demand with unprecedented accuracy. This will enable businesses to optimize inventory levels, reduce carrying costs, and minimize stockouts, improving customer satisfaction and operational efficiency.
The integration of AI in Transportation & Logistics will lead to the widespread adoption of autonomous vehicles, drones, and robotic systems for warehousing and last-mile delivery. We are already seeing businesses where chef to mouth process is either partially or fully automated. In the Warehousing and logistics industry, most of the processes are automated from order entry to pallet, waiting for FedEx or UPS to pick up from the dock door. These technologies have significantly reduced human error, increased operational speed, and enabled 24/7 operations, revolutionizing the way goods are moved and stored. AI-driven predictive maintenance systems will analyze sensor data from equipment and machinery to anticipate potential failures before they occur. This initiative-taking approach will minimize downtime, extend asset lifespans, and optimize maintenance schedules, resulting in substantial cost savings and improved operational reliability.
AI will transform procurement by automating supplier selection, contract negotiations, and purchase order management. Machine learning algorithms will analyze supplier performance, market conditions, and risk factors to make data-driven decisions, ensuring optimal sourcing strategies and cost-effective purchasing. Real-time tracking and visibility capabilities: AI-powered systems will provide end-to-end visibility across the entire supply chain, enabling real-time tracking of goods, assets, and shipments. This enhanced visibility will facilitate better decision-making, improve risk management, and enable rapid response to disruptions or changes in demand.
Significant trends that organizations should anticipate and prepare for include:
The convergence of Digital Twins, AI, IoT and Automation technologies will create a hyper-connected, transparent, and secure supply chain ecosystem. This integration will enable real-time data sharing, enhance traceability, and improved collaboration among stakeholders. AI will play a crucial role in optimizing supply chain operations to reduce carbon footprints, minimize waste, and promote circular economy principles. Organizations will leverage AI to make data-driven decisions that balance economic and environmental considerations.
As AI becomes more prevalent in supply chain operations, organizations will need to attract and retain talent with expertise in data science, machine learning, and AI implementation. Simultaneously, the existing workforce will require continuous upskilling to effectively work alongside AI systems and leverage their capabilities. With the increasing reliance on AI and data-driven decision-making, organizations will need to invest in sophisticated data management systems and cybersecurity measures. This will ensure data integrity, protect sensitive information, and maintain compliance with evolving regulatory requirements.
As AI becomes more pervasive in supply chain operations, organizations will need to develop and adhere to ethical guidelines for AI implementation. This includes addressing concerns related to bias, transparency, and accountability in AI-driven decision-making processes.AI will facilitate the creation of interconnected supply chain networks, fostering collaboration between suppliers, manufacturers, logistics providers, and retailers. These ecosystems will enable seamless information sharing, joint problem-solving, and collective innovation, leading to more resilient and agile supply chains.
To effectively harness the power of AI in supply chain operations, organizations must develop comprehensive strategies that address these trends and advancements. This includes investing in the necessary technology infrastructure, fostering a culture of innovation and continuous learning, and establishing partnerships with AI solution providers and industry experts. By embracing these changes and proactively adapting to the AI-driven future, businesses can position themselves at the forefront of the supply chain revolution, gaining a significant competitive advantage in an increasingly complex and dynamic global marketplace.
What are the biggest challenges organizations face when implementing supply chain digital transformation, and how can they overcome them?
The biggest challenges organizations face when implementing supply chain digital transformation include:
- Resistance to change: Employees may be reluctant to adopt recent technologies and processes. In the last 20+ years, 50+ projects, across several organizations, what I have seen is most business users tend to go back to excel, and it works. Majority of ERP players are trying to build their UIs to look like excel screens.
- Lack of digital skills: Many organizations lack the necessary expertise to implement and manage digital technologies effectively. Project team usually perform basic configurations, training and handing it off to business or relevant IT teams. If the tool is new, there is a learning curve for the business users to know the application.
- Data integration issues: This is a big challenge. Combining data from various sources and legacy systems can be complex and time-consuming.
- Excessive costs: Implementing innovative technologies and training staff can be expensive.
- Cybersecurity concerns: Increased digitalization can expose supply chains to new security risks.
- Complexity of existing systems: Legacy systems may be difficult to integrate with new digital solutions.
To overcome these challenges, organizations can:
Develop a clear digital transformation strategy with defined goals and milestones. Invest in training and upskilling employees to build digital competencies. Prioritize data standardization and integration across the supply chain. Start with small-scale pilot projects to demonstrate value before full-scale implementation. Implement robust cybersecurity measures and regularly assess vulnerabilities. Gradually phase out legacy systems while ensuring smooth transitions to modern technologies. Foster a culture of innovation and continuous improvement to encourage the adoption of digital solutions. Collaborate with technology partners and industry experts to access specialized knowledge and support.
How does data governance impact supply chain efficiency, and what best practices do you recommend for managing master data?
Data quality and integration of relevant data play a critical role, as AI systems rely heavily on accurate, comprehensive information to generate meaningful insights. Organizations should implement robust data governance frameworks, establish data cleansing protocols, and invest in advanced data integration tools to ensure seamless information flow across various supply chain systems. This approach not only improves the accuracy of AI-driven predictions and recommendations but also enhances overall operational efficiency.
Defining and implementing a framework to create, centralize, and comprehensive product repository/hub with associated processes, policies, tools, and people to maintain its integrity. The comprehensive goal should be to extract, transform, use Artificial Intelligence (AI), and build a Decision Data Model, followed by writing those Augmented & Automated Decision data into Global Master Data so that all other downstream processes will have accurate data. Period.
In summary, transformed, fragmented, inconsistent, and inability to scale processes and systems, into a best-in-class, optimized, standardized, and governed process for products and customers coupled with a higher level of centralized data-driven services.
As a best practice, it is important to define.
- Enterprise Data Governance Guiding Principles Framework (Governance Organization, Process Standardization, Data Quality, Asset, Rationalize and only source of truth). These guiding principles should serve as basic and foundational rules within any supply chain organization.
- Define clear roles, responsibilities, and processes for managing master data. This framework should outline data quality standards, data ownership, and procedures.
- Define Data Quality Metrics: Establish key performance indicators (KPIs) to measure the quality of master data. Regularly monitor these metrics to identify data quality issues and track progress in improving data quality.
- Enforce Data Standards: Develop and enforce data standards for all master data elements. These standards should specify data formats, data values, and data validation rules.
Can you share an example of a supply chain transformation initiative you led that had a significant business impact? What were the key factors that made it successful?
Sure, I can discuss a couple of them.
First, I led a green field initiative to revolutionize the Distribution Center operations for the consumer goods industry. Developed an innovative system to optimize inventory allocation, implemented dynamic rule-based replenishment, and integrated AutoStore robotic automation for picking processes. Best in class picking, packing, and conveyor systems are implemented. The approach included designing modular, scalable architecture, ensuring future adaptability and growth, and implementing a phased strategy to minimize disruptions during the transition.
The outcomes were outstanding where order fulfillment errors decreased multifold, transaction processing times reduced significantly, and revenues increased by multi-million. This significant transformation set new industry standards, boosting efficiency and customer satisfaction while improving overall operational capabilities.
Second Initiative: I led a cross-functional initiative to transform our company’s advanced supply chain planning processes and systems. This provided visibility into incoming shipments, enabling customer service to offer accurately Available to Promise (ATP) dates to B2B customers. The goal was to enhance data visibility across various logistic carriers and make the order commitment process transparent and precise. We analyzed milestone data from multiple carriers, adjusted lead times using intelligent rules, bolstered system security, and integrated these insights into our Global Enterprise Resource Planning system.
How can AI and automation be leveraged to enhance supply chain resiliency and adaptability in uncertain market conditions?
Current supply chains are not set up for rapid delivery, customer convenience, or merging distribution channels. Their physical networks and operating models need major changes to adapt and thrive amidst immediate risks and challenges. By leveraging Artificial Intelligence (AI), a Decision Data Model can be built, which can cross the network with automated and augmented decision-making and can provide insights across downstream processes, thereby enhancing operational efficiencies and significantly reducing risk.
The integration of Artificial Intelligence in supply chain management represents a paradigm shift in how organizations approach operational efficiency, resilience, and adaptability. As evidenced by the multifaceted benefits and broad-ranging impacts discussed, AI is not merely a technological upgrade but a strategic imperative for businesses seeking to thrive in an increasingly complex and volatile global marketplace. From enhancing demand forecasting accuracy and optimizing inventory levels to improving fraud detection and streamlining compliance management, AI is proving instrumental in addressing the critical challenges faced by modern supply chains.
As AI technologies continue to evolve and mature, their potential to drive further innovations and efficiencies in supply chain operations is immense. Organizations that successfully leverage AI across the multiple facets of their supply chain management are poised to gain significant competitive advantages, setting new standards for operational excellence, resilience, and customer satisfaction in the digital age.
What role does leadership play in driving digital transformation, and how can technology leaders foster a culture of innovation within their organizations?
As a Leader, communicate transparently, and build, and foster a collaborative workspace. Leadership is crucial in initiating and guiding digital transformation initiatives within organizations. Effective Situational leadership in digital transformation involves setting an unclouded vision and strategy for technological advancement. Transformation is no single dimension. It is multi-dimension, people, process technology are three pillars, and buying in from executive leadership is necessary.
Fast forward, technology will significantly enhance a leader’s ability to communicate, make informed decisions, improve efficiency, support remote work, foster learning, drive innovation, and solve problems. Technology leaders should foster innovation by encouraging experimentation and providing resources for innovative ideas and projects. Fostering a culture of innovation involves creating safe spaces for risk-taking and learning from failures.
Technology leaders should lead, by example, to demonstrate openness to modern technologies and digital solutions. The key is to leverage these tools thoughtfully and strategically to support and advance leadership objectives.
As the Technology Director at Integra LifeSciences, how do you align digital transformation initiatives with the unique challenges and regulatory requirements of the healthcare and life sciences industry?
Whether we agree or not, today’s supply chains remain very volatile. From the ongoing Panama Canal crisis, Tariffs situation, rising inflation, supply shortages, businesses are under tremendous pressure to identify and manage systemic risks in supply chains.
Finished Goods, Raw Materials, Machinery, People and Processes everything can have direct influence on the outcome. For a finished good with multi-layer BOM with an approved supplier for raw material in some regions, changing one ingredient or process in their organization could potentially disrupt the entire supply chain network. Every time there is a change or foresee a change, all the identified products may have to be revalidated and recertified. As a regulated industry it is crucial for us to thoroughly assess our supply chains,and engage with our partners, customers, and suppliers, upstream, and downstream to understand how we can work together to satisfy the regulated (FDA, EUMDR) and local country requirements. A significant part of this effort will involve evaluating the systems we use and what we need to provide along the value chain to ensure compliance between all stakeholders.
This situation could potentially serve as a fortuitous opportunity to delve deeper into innovative technologies such as AI, manufacturing automation, and compliance quality. These advancements can be leveraged to effectively meet the necessary requirements.
How do you evaluate emerging supply chain technologies to determine their real-world applicability and long-term value?
I strongly think creating a culture of data-driven decision-making is an important aspect of any digital transformation. Leaders must assess their readiness for new transformations objectively. They need to balance the pace of technological change with the organization’s capacity to absorb and implement new digital solutions.
To evaluate emerging supply chain technologies, organizations should first conduct thorough research and pilot testing to assess their compatibility with existing systems and processes. It is crucial to analyze the potential return on investment, considering both short-term implementation costs and long-term benefits such as increased efficiency, reduced errors, and improved employee and customer satisfaction.
Engage in collaborative partnerships, webinars, product demos, and research articles, to gain insights into the practical applications and potential limitations of modern technologies before making significant investments.
What are some common pitfalls companies encounter when deploying AI in supply chain management, and how can they be avoided?
Data and process maturity are key. The fundamental question is, are we ready for AI? To successfully deploy AI in supply chain management, companies must address several key challenges. Data quality and integration are paramount, as AI systems rely heavily on accurate, comprehensive information to generate meaningful insights. Organizations should implement robust data governance frameworks, establish data cleansing protocols, and invest in advanced data integration tools to ensure seamless information flow across various supply chain systems. This approach not only improves the accuracy of AI-driven predictions and recommendations but also enhances overall operational efficiency.
Addressing the skills gap is equally crucial for effective AI implementation. Companies should develop comprehensive training programs to upskill existing employees, focusing on areas such as data analytics, machine learning, and AI applications in supply chain contexts. Simultaneously, recruiting AI specialists and data scientists can bring in fresh perspectives and specialized expertise. To overcome resistance to change, organizations must foster a culture of innovation and continuous improvement. This involves clear communication of AI benefits, highlighting early successes, and involving employees in the implementation process. By addressing these challenges proactively, companies can maximize the potential of AI in their supply chain operations, leading to improved forecasting, optimized inventory management, and enhanced decision-making capabilities.
If you had to predict the most disruptive supply chain technology of the next decade, what would it be and why?
AI evolved as a very prominent player in the last couple of years. Drone Adoption and LLM Deployments are getting commercialized at a rapid pace. The workforce will be blended with humans and Digital, where humans’ focus will be more on creative and collaborative tasks while digital can take care of repeated tasks.
Digital twins in supply chains are already being implemented, and it is anticipated that they will become more mature within the next 3-5 years. The global digital twin market is projected to reach $48.2 billion by 2026, driven by the need for real-time monitoring and predictive maintenance across industries. Furthermore, the metaverse has the potential to further accelerate their development.
Digital twins represent a paradigm shift in supply chain management, offering unprecedented levels of visibility, prediction, and optimization. As we have seen, their implementation across various aspects of the supply chain, from demand forecasting to last-mile delivery, has yielded significant benefits in terms of cost reduction, efficiency improvements, and enhanced decision-making. While challenges such as data integration and skill shortages persist, the potential rewards far outweigh the obstacles. Looking ahead, the integration of AI, IoT, blockchain, and extended reality technologies promises to enhance the capabilities of digital twins further, paving the way for more resilient, agile, and intelligent supply networks. As organizations continue to invest in and develop these technologies, we can expect digital twins to play an increasingly vital role in shaping the future of global supply chains, driving innovation, and creating new value across industries.
Enhanced Supply Chain Visibility and Transparency between all the players of the supply chain is necessary. Supply Chain Control Tower is being established and will be a very influential subfunction within the supply chain.
To conclude, the landscape of supply chain management is undergoing a profound transformation driven by emerging technologies and the imperative for greater resilience. We have experienced the current challenges faced by supply chains, including performance metric issues, capacity constraints, and limitations in planning processes.
We have examined how emerging technologies such as robotics, digital twins, cloud-based platforms, and advanced analytics are reshaping supply chain operations, offering new tools to enhance visibility, flexibility, and decision-making capabilities. As supply chains continue to evolve, the integration of these technologies and strategies, coupled with a focus on ethical and sustainable practices, will be crucial in building supply networks capable of withstanding disruptions and adapting to an increasingly complex global environment.
The future of supply chain management lies in the thoughtful application of these innovations, balanced with human expertise and guided by principles of sustainability and ethical responsibility.